Introduction
Control charts are a key tool in statistical process control (SPC) that help monitor and manage a process over time. They provide a visual representation of a process's performance, allowing teams to observe any variations or shifts in the process that may indicate a problem. By plotting data points collected from the process, control charts enable businesses to track the consistency and stability of their operations, helping to identify trends, patterns, or anomalies that may require attention.
The main purpose of control charts is to distinguish between normal, inherent variations in a process (known as common cause variation) and variations caused by specific, identifiable issues (known as special cause variation). By doing so, control charts help organizations determine whether a process is under control or if corrective actions are needed to address deviations. This makes them an essential tool for maintaining process stability, reducing defects, and ensuring that products or services meet quality standards.
Control charts are typically divided into two main components: the central line, which represents the average performance of the process, and the upper and lower control limits, which define the range of acceptable variation. If the data points fall within these limits, the process is considered stable. However, if the points fall outside the limits, it signals a potential issue that requires investigation and corrective action.
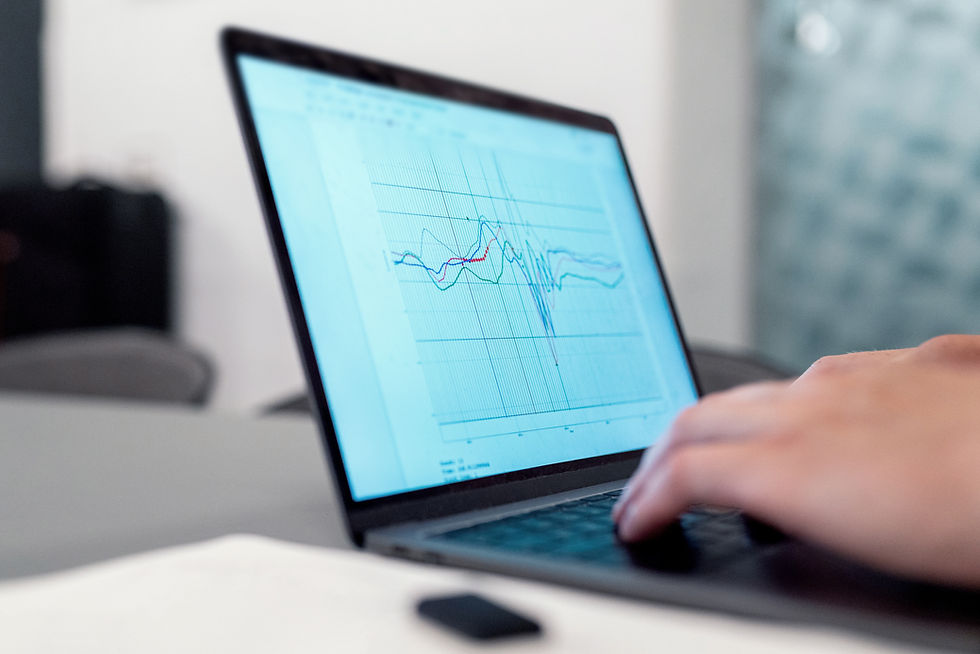
Control charts can be used across a wide range of industries, from manufacturing to healthcare, to monitor various processes such as production lines, service operations, and even customer satisfaction. By providing real-time insights into process performance, control charts enable organizations to make data-driven decisions, reduce variability, and continually improve their operations. Through consistent use, control charts can foster a culture of continuous improvement, where issues are detected early, and processes are fine-tuned to achieve optimal performance.
Control charts are a fundamental tool in statistical process control (SPC), used to track and monitor process performance over time. These charts plot data points sequentially, with the mean, upper control limit (UCL), and lower control limit (LCL) clearly marked on the chart. The mean represents the central tendency of the process data, while the UCL and LCL are determined by the standard deviation and signify the boundaries within which the process should ideally operate. If data points fall outside these boundaries, it indicates that the process has deviated from its expected performance, signaling the need for corrective action.
By continuously tracking the data points and comparing them to the control limits, control charts enable operators to detect when a process is producing results that fall outside the desired range. This allows businesses to identify potential issues early, address them promptly, and prevent the production of non-conforming products or services, ultimately ensuring that the process stays within acceptable quality standards.
There are various types of control charts, each designed for specific types of data and applications. Some of the most commonly used control charts include:
X-bar and R chart: This chart is used to monitor both the central tendency (mean) and the variability (range) of a process, making it useful for processes where multiple samples are taken at regular intervals.
Individual and Moving Range (I-MR) chart: Ideal for processes with small sample sizes (often just one data point at a time), this chart helps monitor process stability over time.
p-chart: Used to track the proportion of defective or non-conforming units in a process, the p-chart is especially valuable when dealing with binary data (e.g., pass/fail).
c-chart: This chart monitors the number of defects or non-conformities per unit within a process, making it suitable for situations where multiple defects may occur in a single item.
Types of Control Charts
Control charts are a powerful tool for continuous improvement and quality control. They help organizations maintain a high level of consistency in their processes, ensuring that products and services meet quality standards. By identifying variations and potential problems early, control charts allow organizations to make informed decisions, improve operational efficiency, and ultimately deliver better value to customers.
Which control charts to use with attribute data and which one to use with continues data?
Control charts are categorized into two types based on the kind of data they monitor: attribute control charts and variable control charts. Each type is suited for different kinds of data, helping to monitor and improve process performance.
Attribute control charts are used for categorical or discrete data, which includes information like the number of defective items or the proportion of non-conforming units in a sample. The two main types of attribute control charts are:
p-chart: This chart monitors the proportion of defective items or non-conforming events in a sample. It is most useful when working with large sample sizes and when the occurrence of defects is relatively low. The p-chart helps track the consistency of the process in terms of product conformity.
c-chart: This chart monitors the count of non-conformities or defects per unit in a sample. It is generally applied when the sample size is small and the likelihood of defects is higher. The c-chart is effective when tracking multiple defects that may occur in a single item or unit.
Variable control charts, on the other hand, are used for continuous or numerical data, such as measurements of product dimensions, weight, or length. The most commonly used variable control charts include:
X-bar and R chart: This chart is used to track both the central tendency (mean) and variability (range) of a process. It is useful when sample sizes are more than one, as it provides insights into how consistent and stable the process is over time.
X-bar and s chart: Similar to the X-bar and R chart, this chart monitors the central tendency and variability of a process, but it uses the standard deviation (s) rather than the range. It is typically used when sample sizes are larger, providing more precise information on process variation.
Individual and Moving Range (I-MR) chart: This chart is employed when sample sizes are small, often with just one data point at a time. It helps track the stability of the process over time, making it particularly useful when monitoring processes with fewer data points.
In conclusion, p-charts and c-charts are used for attribute data, which deal with counts or categories of non-conforming items, while X-bar and R charts, X-bar and s charts, and I-MR charts are used for continuous data, which involve measurements that can take any value within a given range. Each type of chart helps organizations monitor process performance in a way that is appropriate for the data they are working with, ensuring better quality control and improvement.
Comparing table of control charts
TABEL 1
Control Chart | Data Type | Purpose |
p-chart | Attribute | Monitors proportion of non-conforming items or events in a sample |
c-chart | Attribute | Monitors number of non-conformities per unit in a sample |
X-bar and R chart | Variable | Monitors central tendency and variability of a process, based on the mean and range of the sample data |
X-bar and s chart | Variable | Monitors central tendency and variability of a process, based on the mean and standard deviation of the sample data |
Individual and Moving Range (I-MR) chart | Variable | Monitors stability of a process over time when the sample size is one |
Note: There are other types of control charts as well, but these are the most commonly used ones.

Summary
Control charts are essential tools in statistical process control (SPC) used to track and manage a process over time. They help operators monitor the performance of a process, allowing them to detect any deviations or changes from expected performance. This enables proactive adjustments to ensure the process remains stable and within quality standards.
There are two primary categories of control charts: attribute control charts and variable control charts. Attribute control charts are used with categorical or discrete data, while variable control charts are suited for continuous or numerical data.
The most commonly used attribute control charts are the p-chart and the c-chart. The p-chart monitors the proportion of non-conforming items or events in a sample, while the c-chart tracks the number of defects per unit, making it ideal for counting defects in items.
For variable data, the most frequently used control charts include the X-bar and R chart, X-bar and s chart, and the Individual and Moving Range (I-MR) chart. The X-bar and R chart and X-bar and s chart focus on monitoring the central tendency and variability of a process, using the mean and range or standard deviation of sample data, respectively. The I-MR chart is particularly useful for monitoring process stability over time when only one data point is available.
Using control charts effectively allows organizations to detect issues early, improving process consistency and reliability. By continuously tracking performance and addressing deviations, control charts contribute to ongoing process improvement and higher product or service quality.
Control charts are essential quality tools in statistical process control (SPC) used to track and manage a process over time. They help operators monitor the performance of a process, allowing them to detect any deviations or changes from expected performance. This enables proactive adjustments to ensure the process remains stable and within quality standards.
There are two primary categories of control charts: attribute control charts and variable control charts. Attribute control charts are used with categorical or discrete data, while variable control charts are suited for continuous or numerical data.
The most commonly used attribute control charts are the p-chart and the c-chart. The p-chart monitors the proportion of non-conforming items or events in a sample, while the c-chart tracks the number of defects per unit, making it ideal for counting defects in items.
For variable data, the most frequently used control charts include the X-bar and R chart, X-bar and s chart, and the Individual and Moving Range (I-MR) chart. The X-bar and R chart and X-bar and s chart focus on monitoring the central tendency and variability of a process, using the mean and range or standard deviation of sample data, respectively. The I-MR chart is particularly useful for monitoring process stability over time when only one data point is available.
For example,
in the production of water-saving bathtubs, a manufacturer might use a p-chart to track the proportion of bathtubs that meet water-saving standards, ensuring that the products consistently reduce water usage as expected. A c-chart could be used to monitor the number of defects, such as cracks or leaks, per bathtub, helping to maintain high quality in the production process. Additionally, X-bar and R charts could be used to monitor the dimensions of the bathtubs to ensure they conform to specifications while still accommodating water-saving features.
Using control charts effectively allows organizations to detect issues early, improving process consistency and reliability. By continuously tracking performance and addressing deviations, control charts contribute to ongoing process improvement and higher product or service quality. In industries like water and energy conservation, these tools ensure that products like water-saving bathtubs meet both quality and sustainability goals.
(Promoted Affiliate link)
"Every drop counts! Optimize your water use without sacrificing pressure."
Appendix: Control Charts - Explanation and Types
Control charts are essential tools in quality management used to monitor the stability and performance of processes over time. They help detect any variations that may indicate problems in the process, enabling corrective actions before defects occur. Control charts are widely used in Six Sigma, Lean, and other quality improvement methodologies to track the consistency of processes and ensure high-quality outcomes.
What Are Control Charts?
A control chart is a graphical representation of data over time that helps monitor a process’s behavior. It shows how a process performs, identifying whether variations in the output are due to common causes (natural fluctuations) or special causes (uncommon variations or disruptions). Control charts are used to ensure that a process remains stable and operates within predefined control limits.
Key components of a control chart:
Data Points: Represent the values of the process measurements over time.
Central Line: The average or expected value of the data points.
Upper Control Limit (UCL) and Lower Control Limit (LCL): These are the threshold values that indicate whether a process is under control or if there’s an issue requiring corrective action.
Types of Control Charts
Different types of control charts are used depending on the data being analyzed and the type of process being monitored. Below are the most common types:
1. X-bar and R Chart (for Variable Data)
Purpose: Used for monitoring the mean and range of a process when data is continuous (measured in variables).
X-bar Chart: Tracks the average of sample data points over time.
R Chart: Monitors the range (or variation) within the sample data.
When to use: When you are measuring things like weight, temperature, or length, and you have small sample sizes.
2. X-bar and S Chart (for Variable Data)
Purpose: Similar to the X-bar and R chart but used when you have larger sample sizes. The S chart measures the standard deviation of the sample data.
X-bar Chart: Measures the average of the data.
S Chart: Tracks the standard deviation to assess variability.
When to use: When you have large sample sizes (usually greater than 10) and need to track variability more precisely.
3. P Chart (for Attribute Data)
Purpose: Used for monitoring the proportion of defective items in a sample when the data is in the form of pass/fail or defective/non-defective outcomes.
P Chart: Tracks the proportion of defective units in a process.
When to use: When you are monitoring the percentage of defective items in a production process.
4. NP Chart (for Attribute Data)
Purpose: Similar to the P chart, but instead of tracking the proportion, it tracks the number of defective items in a sample.
NP Chart: Monitors the number of defective units in a sample over time.
When to use: When you need to track the number of defects in samples rather than the proportion of defects.
5. C Chart (for Attribute Data)
Purpose: Used to monitor the number of defects per unit of measurement (not the number of defective items). The C chart tracks the count of defects within a specific sample.
C Chart: Monitors the number of defects in a constant sample size.
When to use: When you are tracking defects per item, such as the number of scratches on a part or errors in a document.
6. U Chart (for Attribute Data)
Purpose: Similar to the C chart, but used when the sample size varies. The U chart tracks the number of defects per unit, adjusted for sample size.
U Chart: Monitors the defects per unit with varying sample sizes.
When to use: When the sample size changes from one measurement to the next, and you need to account for this variation.
Useful Links to Top Manufacturers and Resources for Control Charts
Here are some useful links to top manufacturers and resources that utilize control charts and other quality management tools:
1. Toyota - Toyota Production System
Toyota integrates control charts and other quality tools into its Toyota Production System (TPS), focusing on minimizing waste and ensuring that manufacturing processes remain stable and efficient.
2. General Electric (GE) - Lean Six Sigma
General Electric is a leader in Lean Six Sigma practices, including the use of control charts to monitor process stability and improve quality across various industries, from aviation to healthcare.
3. Boeing - Quality and Control in Aerospace Manufacturing
Boeing employs control charts to monitor the quality of their aerospace manufacturing processes, ensuring that every product meets strict safety and performance standards.
4. Ford Motor Company - Quality Management and Control
Ford uses control charts in its manufacturing process to ensure consistent quality in its vehicles, minimizing defects and maintaining high standards of production.
5. 3M - Control Charts for Innovation and Quality
3M applies control charts as part of its commitment to continuous improvement and innovation. The company uses these charts to monitor and optimize processes for consistency and quality in its products.
6. Siemens - Quality Management Systems
Siemens integrates advanced quality management tools, including control charts, into its engineering and manufacturing processes to ensure high standards in its global operations.
7. Honeywell - Operational Excellence and Control Charts
Honeywell uses control charts to monitor and maintain quality in its diverse product lines, which range from industrial equipment to consumer technologies, ensuring consistency and reliability across their offerings.
8. Nestlé - Food Quality and Control
Nestlé applies control charts to maintain quality standards in the food and beverage industry, ensuring that products are produced with high consistency and meet regulatory safety requirements.
These manufacturers exemplify the use of control charts and other quality management tools to maintain high standards of quality, efficiency, and continuous improvement. By exploring their applications, you can gain insights into best practices for using control charts in your own operations.
Thank you for visiting www.robertkurek.com! I truly appreciate you taking the time to explore my insights on water and energy-saving solutions. If you found this post helpful, I encourage you to check out my other articles for more tips and recommendations on creating a sustainable and cost-efficient home or business.
If you need personalized advice or want to learn more about the best water-saving and energy-saving devices for your needs, feel free to contact me or visit my Malvern Aqua Tech website. I’m here to help you make informed choices that will support both your savings and sustainability goals.
Thank you for your commitment to a greener future!
Comments