Continuous Improvement Tools Review
- Robert Kurek
- Jan 12, 2023
- 24 min read
Updated: Dec 31, 2024
In organizations focused on continuous improvement, there are several key tools and methodologies commonly employed to optimize processes, enhance efficiency, and drive higher quality standards. Each of these tools plays a vital role in identifying inefficiencies, reducing waste, and ensuring that operations are aligned with organizational goals. Some of the most significant and widely used tools for continuous improvement include:

Lean:
Lean is a methodology that focuses on streamlining processes by eliminating waste, improving flow, and enhancing value delivery to customers. It’s based on principles such as reducing non-value-added activities, empowering employees, and improving process efficiency. Lean helps organizations create smoother workflows, reduce operational costs, and optimize the use of resources.
Six Sigma:
Six Sigma is a data-driven approach aimed at improving the quality of processes by identifying and eliminating defects. The methodology uses a set of statistical tools to measure process performance, with the goal of achieving near-perfect quality (typically a target of 3.4 defects per million opportunities). Six Sigma emphasizes a structured problem-solving process and a focus on reducing variation in processes, which helps enhance product consistency and reliability.
Theory of Constraints (TOC):
The Theory of Constraints focuses on identifying and addressing the most significant limiting factor (or constraint) that hinders the performance of a system or process. By pinpointing the constraint and optimizing it, organizations can achieve a significant improvement in overall productivity and throughput. TOC helps businesses focus their improvement efforts on the bottleneck that has the largest impact on the system’s performance, leading to more efficient operations.
Statistical Process Control (SPC):
Statistical Process Control is a method used to monitor and control process performance through the use of statistical tools, such as control charts. By continuously measuring key variables and comparing them to established limits, SPC helps identify deviations or potential issues early on. This allows organizations to make adjustments before problems escalate, ensuring that processes stay within desired quality standards and operate efficiently.
Total Quality Management (TQM):
Total Quality Management is an organizational-wide approach that focuses on continuous improvement, customer satisfaction, and the involvement of all employees in quality initiatives. TQM emphasizes a culture of quality, where every department and employee contributes to improving processes, products, and services. It combines various tools and methodologies, such as Lean and Six Sigma, to create a comprehensive approach to improving quality and meeting customer needs.
Together, these tools form a robust framework for organizations aiming to improve their operations. By combining the strengths of each methodology, businesses can ensure they address different aspects of process improvement, from efficiency and quality control to customer satisfaction and overall performance. These tools are integral in helping organizations stay competitive, reduce waste, and drive long-term sustainable growth.
(Promoted Affiliate link)
"Every drop counts! Optimize your water use without sacrificing pressure."
Introduction
Lean, as a continuous improvement methodology, is a management approach designed to maximize value while minimizing resources. Initially developed in the manufacturing industry, Lean has expanded its application to various fields, including healthcare, service sectors, and even government operations.
At its foundation, Lean focuses on eliminating waste in all areas of the production process. This waste can take many forms, including excess inventory, overproduction, unnecessary waiting times, inefficient transportation, defects, over-processing, and underutilized talent. By identifying and removing these inefficiencies, Lean helps organizations increase productivity, improve quality, and ultimately deliver more value to customers.
In practical terms, Lean utilizes a variety of tools and techniques to identify inefficiencies and streamline processes. These tools include value stream mapping, which visually represents the steps involved in a process to identify waste; Kaizen, a philosophy of continuous, incremental improvements; Just-in-Time (JIT) production, which focuses on producing goods only as needed; and visual management, which uses visual cues to manage processes more effectively. Together, these methods help organizations spot and address inefficiencies, ensuring smoother operations and empowering employees to contribute to improvements.
The ultimate goal of Lean is to foster a culture of continuous improvement. This involves engaging employees at all levels to actively identify waste and contribute to enhancing processes. By creating a focus on customer value, streamlining operations, and empowering the workforce, Lean aims to build a more efficient, effective, and customer-centered organization, better equipped to meet the needs of both customers and stakeholders.

History of Lean (Continuous Improvement Tools).
Lean has its origins in the Japanese manufacturing industry, specifically developed by Toyota during the 1950s and 1960s. Initially known as the Toyota Production System (TPS), it was created by Toyota’s founder Sakichi Toyoda, his son Kiichiro Toyoda, and one of their leading engineers, Taiichi Ohno. The TPS was a response to Japan’s post-World War II economic challenges, such as a shortage of resources and capital. Toyota needed a way to overcome these constraints and compete with larger, more established Western automakers.
The key principles behind the TPS were designed to increase efficiency and reduce waste. Concepts such as Just-In-Time (JIT) production, which aims to produce only what is needed when it is needed, and standardized work were core to the system. The emphasis was also placed on continuous improvement, which encouraged ongoing refinement of processes and products.
As the TPS gained success, it was later referred to as lean production, and its principles spread beyond Japan. Researchers like James Womack and Daniel Jones helped popularize these ideas outside of Japan with the release of their influential 1990 book, "The Machine That Changed the World." This book highlighted Toyota’s success and introduced the concept of lean production to a global audience, showcasing how its principles could transform businesses in various sectors.
Today, lean is widely recognized not just in manufacturing, but across industries such as healthcare, services, and government, where it’s used to improve efficiency, minimize waste, and create greater value for customers. The impact of lean continues to grow globally, with organizations adopting it as a powerful management philosophy to drive continuous improvement and enhance operational effectiveness.
Lean Philosophy
The lean philosophy is a management approach that focuses on delivering value to customers while minimizing waste in all its forms. It operates on the principle that every non-value-adding activity in a process should be identified and eliminated, while value-adding activities should be optimized to maximize efficiency and effectiveness. At its heart, lean centers around five fundamental principles that guide organizations in their pursuit of greater productivity and customer satisfaction.
Define value from the customer's perspective: Value is defined as anything that a customer is willing to pay for, so organizations must understand their customers' needs and expectations to provide them with true value. This ensures that all efforts are aligned with what matters most to the customer.
Identify the value stream: The value stream refers to the series of steps involved in delivering a product or service to the customer. By mapping out and evaluating each step in the value stream, organizations can pinpoint areas where waste exists, such as unnecessary movements or delays, and work to eliminate them.
Create flow: Lean focuses on achieving a smooth, continuous flow of value-adding activities throughout the value stream. This involves eliminating bottlenecks, reducing waiting times, and improving process steps to ensure that work flows seamlessly from one task to the next without interruptions.
Establish pull: In a lean system, production is driven by customer demand. Products and services are only created when needed, which helps prevent overproduction and reduces excess inventory. This principle requires organizations to be flexible and responsive to changes in customer needs, ensuring that resources are used efficiently.
Pursue perfection: Lean is a continuous improvement journey aimed at achieving perfection in quality, speed, and efficiency. Organizations must foster a culture of ongoing improvement, where every employee is encouraged to identify waste, suggest improvements, and help refine processes. This drive for perfection ensures that the organization remains agile and competitive.
Lean Philosophy
By adhering to these principles, organizations can build a culture of continuous improvement that enhances efficiency, improves quality, and delivers greater value to customers. Lean is not just a set of techniques or tools—it’s a comprehensive management approach that can be implemented across industries to drive sustainable growth and success.
Lean Benefits
Implementing a lean approach to production offers numerous benefits for organizations, helping to streamline operations, reduce waste, and improve overall performance. Some of the key advantages of adopting lean principles include:
Increased Efficiency: By identifying and eliminating wasteful practices, lean helps organizations optimize their processes, leading to faster production cycles, reduced lead times, and better throughput. This optimization makes the production process more efficient, allowing organizations to meet customer demands more effectively.
Improved Quality: Lean principles prioritize quality and continuous improvement. By focusing on eliminating defects and errors, organizations can enhance the quality of their products and services. This leads to lower defect rates, reduced rework, and higher customer satisfaction, which in turn boosts the reputation of the company.
Reduced Costs: Lean helps organizations cut unnecessary costs by improving efficiency and eliminating waste. Savings can be achieved in various areas, such as reduced inventory levels, better asset utilization, and decreased labor costs. These cost reductions contribute directly to improving profitability and financial sustainability.
Improved Customer Satisfaction: Since lean is focused on delivering value to customers, it naturally leads to higher levels of customer satisfaction. By understanding customer needs and responding quickly to changes in demand, organizations can ensure that they meet customer expectations consistently. This responsiveness strengthens customer loyalty and gives the organization a competitive edge.
Empowered Employees: Lean encourages employee involvement in problem-solving and continuous improvement efforts. By empowering employees to identify issues and suggest solutions, organizations can foster a culture of collaboration, which leads to improved morale, job satisfaction, and engagement. Employees feel more valued and motivated, contributing to a positive work environment.
Flexibility and Agility: Lean systems are designed to be responsive and adaptable to changes in demand or market conditions. By using pull systems and producing only what is needed, organizations can avoid overproduction and quickly adjust to shifts in customer preferences or demand. This flexibility allows businesses to remain agile in a fast-paced and dynamic marketplace.
Overall, implementing lean can help organizations improve efficiency, quality, and customer satisfaction, while reducing costs and waste. However, to fully benefit from lean, organizations must commit to continuous improvement and embrace change, experimentation, and innovation as part of their ongoing development.
Six Sigma History
Six Sigma is a quality management methodology that was developed by Motorola in the mid-1980s to address product quality issues and reduce defects in manufacturing processes. The term "Six Sigma" refers to a statistical measure of process variability, aiming to reduce this variability to a level where there are no more than 3.4 defects per million opportunities, a standard representing near-perfect quality.
The methodology was created by a team of engineers, led by Bill Smith, who worked in Motorola’s quality department. The team recognized that many of the quality issues in their manufacturing processes were caused by variability. To tackle this problem, they designed a structured, data-driven approach to problem-solving that focuses on identifying, measuring, and eliminating the root causes of defects.
Key tools and techniques in Six Sigma include statistical process control, process mapping, and root cause analysis. These tools help to identify areas of variation and inefficiencies, guiding organizations to improve their processes and eliminate defects.
Following its success at Motorola, Six Sigma was popularized in the 1990s by Jack Welch, the CEO of General Electric (GE). GE made Six Sigma a central part of its business strategy, claiming billions of dollars in savings as a result. Since then, Six Sigma has expanded beyond manufacturing to be applied in a wide range of industries, such as healthcare, finance, and government. Over time, the methodology has evolved to incorporate a greater focus on customer needs and overall process improvement.
Six Sigma Philosophy:
The philosophy behind Six Sigma is rooted in data-driven decision-making and a focus on reducing defects and variability across all business processes. It aims to improve performance by cutting costs, enhancing customer satisfaction, and boosting productivity.

The key principles of Six Sigma are:
Focus on the Customer: The methodology places great emphasis on understanding and meeting the needs of customers. Ensuring that products and services align with customer expectations is a priority.
Data-Driven Decision Making: Decisions within Six Sigma are based on data and statistical analysis. This involves collecting and analyzing data on process performance to identify variability and defects, allowing organizations to make informed decisions about improvements.
Continuous Improvement: Six Sigma is centered around the goal of continuous improvement. The objective is to achieve near-perfect quality across all processes, which requires creating a culture of ongoing evaluation, feedback, and refinement. Employees are encouraged to identify areas for improvement and eliminate waste.
Leadership Involvement: Successful implementation of Six Sigma requires strong commitment and active involvement from leadership. Leaders must provide the necessary resources and support and ensure they are engaged throughout the process.
Teamwork: Six Sigma promotes collaboration across teams and departments. Cross-functional teams work together to identify problems, solve them, and drive improvements throughout the organization.
By adhering to these principles, organizations can foster a culture of continuous improvement, which leads to enhanced efficiency, better quality, and more value for customers. Six Sigma is not just a set of tools but a comprehensive management approach that can be applied across various industries and sectors, enabling businesses to consistently improve and achieve excellence.

Six Sigma Benefits
The benefits of implementing a Six Sigma approach to quality management can be significant for organizations. Some of the key benefits of Six Sigma include:
Improved quality: Six Sigma aims to reduce defects and variability in business processes, which can lead to higher quality products and services. This can result in improved customer satisfaction, and can also reduce costs associated with rework, returns, and warranty claims.
Reduced costs: By identifying and eliminating sources of waste and inefficiency, Six Sigma can help organizations reduce their costs. This can include savings from reduced inventory, improved asset utilization, and reduced labor costs.
Increased efficiency: Six Sigma focuses on optimizing processes and eliminating waste, which can lead to improved efficiency and faster production times. This can help organizations reduce lead times, increase throughput, and respond more quickly to changes in demand.
Improved customer satisfaction: By focusing on meeting customer needs and expectations, Six Sigma can help organizations improve customer satisfaction and loyalty. This can lead to increased repeat business, referrals, and a stronger reputation in the market.
Better decision-making: Six Sigma relies on data and statistical analysis to make decisions, which can lead to more informed and objective decision-making. This can help organizations make better strategic decisions, and can also facilitate continuous improvement by identifying areas for improvement.
Improved employee engagement: Six Sigma encourages employee involvement and participation in continuous improvement efforts. By empowering employees to identify and solve problems, organizations can improve employee morale, engagement, and job satisfaction.
Overall, implementing a Six Sigma approach can help organizations create more value for their customers, reduce waste, and improve their bottom line. However, it requires a commitment to continuous improvement and a willingness to embrace change and experimentation.
Theory of Constraints
The Theory of Constraints (TOC) is a management philosophy developed by Eliyahu Goldratt in the 1980s. It focuses on identifying and eliminating the bottlenecks, or constraints, that limit the performance of a system. This approach has been widely applied across various industries and organizations to improve operational efficiency.
At its core, the Theory of Constraints suggests that every system has one or more constraints that restrict its overall output. These constraints can be physical, such as equipment limitations, or they can be related to policies, procedures, or market demand. By pinpointing and addressing these bottlenecks, organizations can enhance the performance of the entire system.
The TOC methodology follows a five-step process for improving system performance:
Identify the system's constraints: The first step is to identify the factors that limit the performance of the system. These constraints could be anything from equipment failures to outdated policies or insufficient demand. Recognizing these limitations is essential for improvement.
Decide how to exploit the system's constraints: Once the constraints are identified, the next step is to find ways to maximize the output of these limiting factors. This could involve strategies like increasing capacity, optimizing processes, or reducing downtime.
Subordinate everything else to the above decision: All other processes and activities within the system should be aligned to support the exploitation of the constraints. This means that non-critical areas of the system may need to be adjusted or prioritized to ensure that resources are being focused on the constraint.
Elevate the system's constraints: The next step involves permanently increasing the capacity of the constraint. This could mean investing in new equipment, upgrading technology, or reorganizing resources to improve the constraint’s output.
Repeat the process: After the first constraint has been addressed, the process is repeated to identify and resolve the next bottleneck. This ensures that improvements are ongoing and that the system’s overall performance continues to improve.
Theory of Constraints
The Theory of Constraints emphasizes the importance of viewing the system as a whole, rather than optimizing individual components. By focusing on the constraints that limit performance, organizations can achieve greater efficiency, productivity, and profitability. This holistic approach ensures that the system as a whole functions optimally, rather than just improving isolated parts.
Statistical Process Control
Statistical Process Control (SPC) is a method used for quality control that employs statistical techniques to monitor and manage a process. The approach involves gathering data on the output of a process and using statistical analysis to assess whether the process is operating within predefined acceptable limits. The main aim of SPC is to ensure that the process consistently produces products or services that meet customer requirements, all while minimizing waste and reducing costs.
SPC works by tracking data over time to identify trends, patterns, and variations that may suggest the process is either unstable or producing inconsistent results. This helps businesses detect potential issues early, allowing them to take corrective action before problems escalate.
The key steps involved in SPC include:
Identifying Critical Characteristics: The first step is to determine which aspects of the process are critical to maintaining product quality. These are the characteristics that must be monitored closely to ensure that the process meets customer expectations.
Establishing a Data Collection System: A system is set up to gather data on the process output. This data is necessary for analyzing the performance of the process and detecting any variations.
Plotting Data on a Control Chart: The collected data is then plotted on a control chart, a graphical representation that shows how the process performs over time. The chart helps visualize whether the process remains stable or whether variations are occurring.
Analyzing the Control Chart: The control chart is examined to identify trends or patterns. Key analysis points include checking whether the process is stable or unstable, determining if there are special causes of variation, and verifying whether the process stays within acceptable limits.
Taking Corrective Action: If the analysis reveals that the process is out of control or producing products that fall outside of specifications, corrective action is taken to bring the process back into alignment. This ensures that quality is maintained and any issues are promptly addressed.
SPC is extensively used across industries such as manufacturing, healthcare, and more, wherever consistent quality is a priority. It is also an essential tool within methodologies like Lean Six Sigma and other process improvement initiatives. By applying statistical methods to monitor and control processes, SPC helps organizations not only improve product quality but also reduce waste, lower costs, and ultimately boost customer satisfaction.
Total Quality Management
Total Quality Management (TQM) is a comprehensive management philosophy that focuses on involving all employees within an organization in a continuous process of improvement. The ultimate goal of TQM is to meet or exceed customer expectations by delivering products and services of the highest quality.

TQM emphasizes a customer-focused approach, recognizing that quality must be integrated into every aspect of the organization, from design and production to marketing and customer service. The key principles of TQM include:
Continuous Improvement: TQM stresses the need for ongoing improvements in all processes, products, and services. This principle advocates for regular measurement, analysis, and adjustments to ensure that customer requirements are consistently met. It fosters a culture where quality is continuously enhanced.
Customer Focus: Central to TQM is the commitment to understanding and meeting customer needs. This involves actively gathering customer feedback and using that data to refine and improve products and services, ensuring that the final outcome aligns with customer expectations.
Employee Involvement: TQM encourages the participation of all employees in the quality improvement process. This means providing training on quality management principles and equipping employees with the tools and resources needed to identify and resolve process inefficiencies, fostering a sense of ownership in the organization's success.
Leadership Commitment: Successful implementation of TQM requires strong support and commitment from top management. Leaders set the direction by defining the organization's vision, values, and objectives, and ensure the necessary resources and support are available to implement quality initiatives across the organization.
Process Approach: TQM uses a process-oriented approach to quality management, focusing on systematically analyzing and improving processes to achieve optimal results. By looking at processes in their entirety, TQM ensures that improvements are made holistically rather than in isolation.
Data-Driven Decision Making: TQM relies heavily on data and statistical analysis to guide decisions on quality improvement. Tools like statistical process control and quality control charts are used to monitor processes, identify trends, and make informed decisions aimed at improving overall quality.
Overall, TQM is a holistic approach that involves every part of an organization, from leadership to employees, in the pursuit of continuous improvement. By aligning processes with customer needs and focusing on ongoing enhancement, TQM helps organizations reduce waste, lower costs, and improve customer satisfaction, ultimately leading to sustained business success.
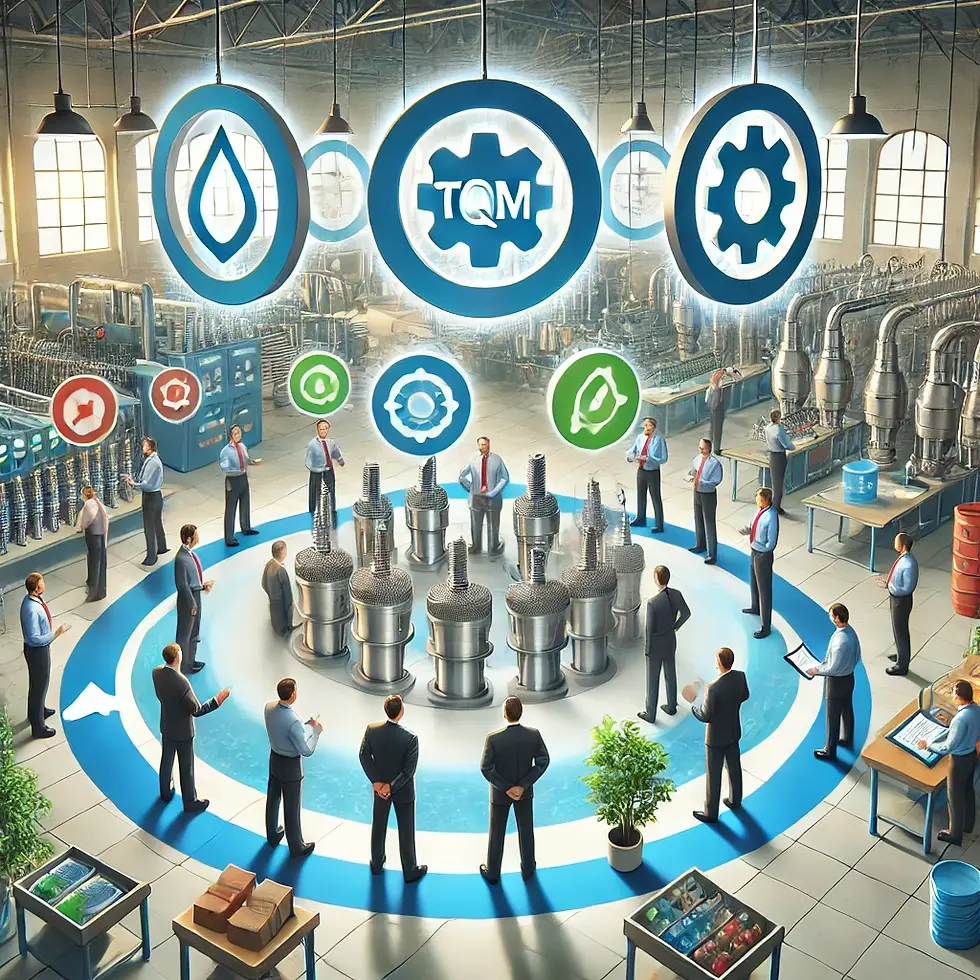
Comparison of Lean, Six Sigma, Theory of Constraints, Statistical Process Control, Total Quality Management as Improvement Tools
Lean, Six Sigma, Theory of Constraints (TOC), Statistical Process Control (SPC), and Total Quality Management (TQM) are all powerful improvement tools used by organizations to enhance quality, reduce waste, and increase efficiency. While each approach has its own unique characteristics, they share a common goal of process optimization and performance improvement. Here’s a comparison of these tools and their distinct features:
Lean: Lean is a systematic methodology focused on identifying and eliminating waste within processes. Its core principle is the continuous improvement of processes by eliminating non-value-added activities. Lean emphasizes reducing waste, optimizing process flow, and improving efficiency. Key tools include value stream mapping, kaizen events, and visual management, all aimed at streamlining operations and ensuring that resources are used as effectively as possible.
Six Sigma: Six Sigma is a data-driven approach designed to reduce defects and minimize variation within processes. It relies heavily on statistical analysis to pinpoint the root causes of quality issues and improve consistency. Six Sigma aims to enhance quality, reduce defects, and increase process efficiency by focusing on minimizing variation. Its core methodology is DMAIC (Define, Measure, Analyze, Improve, Control), supported by tools like statistical process control and various data analysis techniques to optimize process performance.
Theory of Constraints (TOC): The Theory of Constraints focuses on identifying and improving the weakest link (or constraint) in a process to increase the system’s overall throughput. TOC seeks to enhance flow and reduce bottlenecks, aiming for smoother processes and greater output. It is structured around the Five Focusing Steps, buffer management, and the Drum-Buffer-Rope system, which work together to ensure that constraints are identified, managed, and optimized for maximum system-wide performance.
Statistical Process Control (SPC): SPC is a quality control method that uses statistical tools to monitor and control a process. By collecting data on process outputs and analyzing it statistically, SPC helps determine whether a process is operating within acceptable limits. SPC focuses on reducing process variation, improving quality, and enhancing efficiency. Tools used in SPC include control charts, histograms, and Pareto charts, which assist in identifying trends, understanding process behavior, and ensuring consistent quality.
Total Quality Management (TQM): TQM is a comprehensive, organization-wide approach to improving quality, with a strong focus on customer satisfaction. It involves everyone in the organization in the quality improvement process, emphasizing continuous improvement, employee involvement, leadership commitment, and a focus on processes. TQM’s tools include quality circles, process mapping, and employee training, and its goal is to create a culture of quality that integrates customer needs into every aspect of the organization.
In summary, while Lean, Six Sigma, TOC, SPC, and TQM each have unique strengths, they all focus on improving efficiency, reducing waste, and enhancing quality. Organizations may choose one or more of these tools based on their specific needs, goals, and the nature of their processes. Each methodology provides valuable insights and strategies for optimizing operations, and the best results often come from combining elements of these approaches to address a wide range of business challenges.
Real Life Example
Using Quality Tools in Manufacturing: Manufacturing on Saving-Water Aerators.
In the manufacturing of water-saving aerators, which are devices installed in faucets and showerheads to reduce water flow without sacrificing water pressure, various continuous improvement tools like Lean, Six Sigma, Theory of Constraints (TOC), Statistical Process Control (SPC), and Total Quality Management (TQM) can be applied to enhance production efficiency, improve product quality, and meet customer demands for eco-friendly, cost-effective solutions. Here's how these tools could be used in practice:
Lean in Water-Saving Aerators Manufacturing:
Lean focuses on eliminating waste and improving process flow. In manufacturing water-saving aerators, Lean principles can help optimize production processes, reduce excess inventory, and improve lead times. For example:
Value Stream Mapping can be used to map out the entire production process, from raw material procurement (such as specialized materials for aerators) to final assembly and packaging. The goal is to identify areas where waste occurs, such as overproduction, waiting times, or unnecessary transportation, and then eliminate or streamline these steps.
Kaizen events could be implemented where teams focus on making small, continuous improvements in production, such as optimizing the assembly line or reducing downtime during machine changeovers.
Visual Management could be used to create visual cues on the production floor to highlight bottlenecks or areas where resources need to be allocated more efficiently.
Six Sigma in Water-Saving Aerators Manufacturing:
Six Sigma focuses on reducing defects and process variation, which is crucial in producing water-saving aerators that perform consistently and meet strict quality standards.
DMAIC (Define, Measure, Analyze, Improve, Control) could be used to address a specific problem, such as variation in the aerator’s water flow rate.
In the Measure phase, data could be gathered on the performance of the aerators to identify any defects or inconsistencies in water flow.
In the Analyze phase, statistical tools would be used to determine the root cause of any variation, such as inconsistent aerator design or issues during manufacturing.
In the Improve phase, solutions like design adjustments or improved production methods could be implemented to standardize quality and ensure the aerators consistently meet the desired water flow rate.
Control Charts would be used in the Control phase to monitor the performance of aerators over time, ensuring that they consistently meet the required specifications.
Theory of Constraints (TOC) in Water-Saving Aerators Manufacturing:
TOC focuses on identifying and addressing the bottleneck or constraint in the production process to improve overall throughput. In the case of water-saving aerators, the constraint could be in the assembly stage, where certain machines or parts slow down the entire production line.
Five Focusing Steps could be applied:
Identify the Constraint: Through analysis, the team might find that the testing phase, where each aerator is tested for water flow and quality, is slowing down production.
Exploit the Constraint: To maximize the output, the team might improve the efficiency of the testing process, such as automating part of the testing or streamlining setup times.
Subordinate Everything Else: Other stages of production, like molding and assembly, could be adjusted to align with the capacity of the testing phase, ensuring that the bottleneck is effectively managed.
Elevate the Constraint: To permanently address the bottleneck, additional testing equipment or improved methods could be introduced.
Repeat the Process: Once the testing bottleneck is resolved, the next constraint in the production line would be identified and addressed.
Statistical Process Control (SPC) in Water-Saving Aerators Manufacturing:
SPC is used to monitor and control process performance through statistical methods, ensuring that the aerators meet quality standards consistently.
Control Charts could be used to track key production metrics, such as water flow rate or aerator durability. By continuously collecting data on these variables, manufacturers can spot deviations from the desired performance and take corrective actions before large batches of defective aerators are produced.
Pareto Analysis could be used to identify the most common defects in the aerators (e.g., inconsistent water flow or poor sealing) and focus improvement efforts on the most significant issues, thereby increasing overall quality.
Total Quality Management (TQM) in Water-Saving Aerators Manufacturing:
TQM emphasizes a holistic, organization-wide approach to improving quality and meeting customer expectations. In the case of water-saving aerators, TQM could be used to create a culture where everyone in the organization—from the design team to the production floor to customer service—is involved in quality improvement.
Customer Focus: By gathering feedback from customers regarding the performance of aerators (e.g., water savings, durability), the company can continuously improve product design and functionality.
Employee Involvement: Employees at all levels could be trained in quality management techniques and encouraged to participate in problem-solving efforts. For instance, workers on the production line could be empowered to identify inefficiencies or quality issues, making improvements to the process.
Continuous Improvement: A culture of continuous improvement would be nurtured by regularly reviewing performance data, conducting regular meetings, and using tools like quality circles to foster collaboration on solving quality issues.
Process Mapping and Root Cause Analysis could be employed to identify weak points in production and refine processes to minimize defects and ensure that the final product is of the highest quality.
Summary:
By integrating tools such as Lean, Six Sigma, TOC, SPC, and TQM, the manufacturing process of water-saving aerators can be significantly optimized. Lean can help streamline operations and eliminate waste, Six Sigma ensures product consistency and defect reduction, TOC focuses on resolving production bottlenecks, SPC monitors process stability, and TQM creates a culture of continuous quality improvement. Using these tools together, manufacturers can improve product quality, reduce waste, enhance customer satisfaction, and increase overall efficiency in the production of energy-efficient, high-quality water-saving aerators.
(Promoted Affiliate link)
"Every drop counts! Optimize your water use without sacrificing pressure."
Appendix: Continuous Improvement Tools Review
In addition to water and energy-saving practices, adopting continuous improvement tools in both home and business operations can lead to greater efficiency and sustainability. Continuous improvement tools are designed to help organizations and individuals identify areas for improvement, reduce waste, and optimize processes. Below is a review of some of the most effective continuous improvement tools that can help improve resource conservation and drive positive environmental impact.
1. The PDCA Cycle (Plan-Do-Check-Act)
The PDCA Cycle is one of the most well-known continuous improvement tools. It's a systematic method for solving problems and improving processes that can be applied to virtually any aspect of life, from business operations to water conservation efforts.
Plan: Identify opportunities for improvement (e.g., saving water and energy in your home).
Do: Implement the changes on a small scale (e.g., installing water-saving showerheads or energy-efficient lighting).
Check: Evaluate the results to see if the changes were effective.
Act: If successful, standardize the changes across all areas; if not, revisit the plan and adjust as needed.
The PDCA cycle fosters a culture of continuous learning and improvement, ensuring that you're always striving for better efficiency and sustainability.
2. Six Sigma
Six Sigma is a data-driven methodology focused on reducing defects and improving processes. It uses statistical analysis to identify root causes of problems and helps businesses implement strategies to achieve consistent and high-quality results. While typically used in large-scale business settings, Six Sigma can also be applied to smaller operations, such as reducing water and energy waste in a household or small business.
Define: Clearly identify the problem or area for improvement (e.g., excessive water usage).
Measure: Collect data to understand the scope of the issue.
Analyze: Use tools like Pareto analysis or root cause analysis to find underlying causes.
Improve: Implement solutions to address the root causes.
Control: Put measures in place to ensure improvements are sustained.
By applying Six Sigma principles, you can streamline processes and reduce unnecessary consumption of water and energy.
3. Kaizen (Continuous Improvement)
Kaizen is a Japanese term that means "change for better" or "continuous improvement." It encourages small, incremental changes over time that result in significant improvements. In the context of resource conservation, Kaizen could involve regularly reviewing energy and water consumption habits and making small adjustments to improve efficiency.
Focus on incremental improvements: Rather than making drastic changes, Kaizen emphasizes gradual, manageable changes.
Involve everyone: From homeowners to business staff, everyone contributes to finding and implementing improvements.
By applying Kaizen, you can foster a culture of sustainability where everyone plays a role in making the world a greener place.
4. Value Stream Mapping
Value Stream Mapping (VSM) is a tool used to visually map the flow of materials and information throughout a process. While it’s often used in manufacturing to identify inefficiencies, it can also be applied to everyday operations, such as monitoring the water or energy consumption in a home or business. The goal is to identify and eliminate waste, creating a more streamlined, efficient system.
Map the process: Draw a flowchart of water and energy use in your home or business.
Identify waste: Look for steps where excess water or energy is being used unnecessarily.
Optimize: Implement changes to minimize waste and increase efficiency.
Through VSM, you can gain a clearer understanding of how resources are used and identify areas where you can improve.
5. 5S (Sort, Set in Order, Shine, Standardize, Sustain)
The 5S methodology is a workplace organization method that helps improve efficiency and reduce waste by ensuring everything has a place and is kept in an optimal condition. While traditionally used in manufacturing settings, it can also be applied to reduce resource waste at home or in business operations.
Sort: Remove unnecessary items (e.g., old appliances that use excessive water or energy).
Set in Order: Organize items for easy access and use (e.g., place water-efficient devices where they are easily accessible).
Shine: Regularly clean and maintain appliances and fixtures to ensure they are operating at peak efficiency.
Standardize: Set procedures for reducing waste and conserving resources.
Sustain: Create a habit of consistently following the new practices.
The 5S methodology creates a cleaner, more efficient environment, which ultimately leads to reduced waste and improved resource usage.
6. Root Cause Analysis (RCA)
Root Cause Analysis is a problem-solving tool used to identify the fundamental causes of issues. If you're struggling with high water or energy bills, RCA can help uncover the reasons behind excessive consumption, whether it's due to outdated appliances, inefficient habits, or faulty equipment.
Identify the problem: For example, excessive water usage during showers.
Investigate the causes: Look for leaks, inefficient showerheads, or habits like running water unnecessarily.
Implement corrective actions: Replace faulty fixtures, install water-saving devices, or adjust usage habits.
RCA helps you understand the "why" behind your resource consumption and implement lasting solutions.
Conclusion
Using these continuous improvement tools, homeowners and business owners can actively work toward reducing water and energy consumption while optimizing overall efficiency. Whether you're looking to adopt lean practices at home or in your business, these tools provide a structured approach to achieving your sustainability goals. By committing to regular assessment and improvement, you can ensure that you're making the best use of your resources—today and for the generations to come.
Here are some useful links to further explore the topic of saving water, energy, and continuous improvement tools:
Water and Energy Saving Resources:
U.S. Environmental Protection Agency (EPA) - WaterSense https://www.epa.gov/watersense The EPA’s WaterSense program offers a variety of water-saving tips and tools, including information on water-efficient products like showerheads, faucets, and toilets.
Energy Star - Save Energy at Home https://www.energystar.gov/ Energy Star provides energy-saving tips for homes and businesses, including recommendations on appliances, lighting, and heating and cooling systems.
The Water Project https://www.thewaterproject.org/ A nonprofit dedicated to providing clean water to communities in need. They offer educational resources on water conservation and the importance of water management.
Home Energy Saver (U.S. Department of Energy) https://hes.lbl.gov/ A tool to help homeowners identify ways to save energy and reduce their utility bills through various efficiency improvements.
Continuous Improvement Tools:
American Society for Quality (ASQ) - PDCA Cycle https://asq.org/quality-resources/pdca-cycle ASQ provides an in-depth look at the PDCA cycle, including how to apply it in various settings, from manufacturing to home improvements.
Six Sigma Institute https://www.sixsigmainstitute.org/ A comprehensive resource for learning about Six Sigma methodologies and how they can be applied to improve processes in different industries.
Lean Enterprise Institute (Kaizen & Lean Tools) https://www.lean.org/ The Lean Enterprise Institute offers resources and insights into Kaizen, Lean tools, and continuous improvement strategies to optimize processes and reduce waste.
Value Stream Mapping Resources (GoLeanSixSigma) https://www.goleansixsigma.com/value-stream-mapping/ GoLeanSixSigma provides detailed guides and templates for implementing Value Stream Mapping to identify waste and improve processes in any organization.
5S Resources - Lean Production https://www.leanproduction.com/5s/ This site covers the 5S methodology and how it can be applied to improve efficiency in various settings, from manufacturing floors to homes and businesses.
General Sustainability and Resource Management:
Sustainable Living Guide (Green America)
https://www.greenamerica.org/sustainable-living
Green America offers tips and resources for sustainable living, including advice on energy, water conservation, and eco-friendly practices for businesses and homes.
By exploring these links, you’ll gain a deeper understanding of both the practical steps for reducing water and energy usage and the continuous improvement tools that can enhance efficiency in your daily life or business operations.
Thank you for visiting www.robertkurek.com! I truly appreciate you taking the time to explore my insights on water and energy-saving solutions. If you found this post helpful, I encourage you to check out my other articles for more tips and recommendations on creating a sustainable and cost-efficient home or business.
If you need personalized advice or want to learn more about the best water-saving and energy-saving devices for your needs, feel free to contact me or visit my Malvern Aqua Tech website. I’m here to help you make informed choices that will support both your savings and sustainability goals.
Thank you for your commitment to a greener future!
コメント