
MY BIO
Who I Am
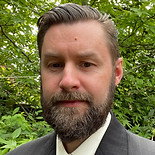
I am a qualified, responsible person and believe my education and employment background are appropriate for QE specialising in Water and Energy Saving Products / Systems.
I am independent, result-oriented and open-minded person eager to learn new things and striving for continued excellence. I am strongly convinced that my background is in perfect line with your current needs and that I can apply my knowledge and skills to improve quality.
'I have dedicated 15 years of my professional career to be part of the most exciting projects related to developing Water and Energy Saving products.
Why?
Because Water is Our most valuable resource.
Because I believe We can together Save Our Planet for next Generations!'
As a Quality Engineer I am responsible for overseeing the Quality Control and Assurance activities relating to the Assembly, Automation and Logistics processes.
Tasks and Responsibilities:
Provide general support, including absence cover to the Quality Manager, as well as:
Product Quality
• Validate process changes, including introduction of new equipment.
• Monitor and report process average defective levels, setting risk-based priorities for improvement actions.
• Work with the automation department to identify root causes of non-conformance and validate actions taken.
• Document actions taken to eliminate non-conformity.
• Write work instructions, operational control procedures
• Monitor and report the incoming quality of components from internal and external suppliers, including sub-contractors, and implement actions needed to eliminate non-conformity.
Customer Complaints (To maintain customer confidence, and the company’s reputation)
• External Communication with customers
• Internal communication
• Investigation including usage of quality tools and documenting results
• Carry out containment actions in the case of customer complaints or internal non-conformance.
• Assist with the investigation of customer complaints.
• Assist with the internal audit processes
• Process customer returns.
• Update operational control plans.
Production Realise (New Product Introduction) (To make sure production have all the necessary information to produce products)
• Archiving and Managing documentation related to NPI and updates to QMS
• Updating Quality Plans
• Updating and maintaining Test procedures and templates
• Internal communication with involved parties
Purchased Goods (To ensure that purchased goods meet our requirements, that inspection costs are kept to a minimum and information about supplier performance is available)
• Deciding which products needs checking and control (looking at risk, risk managing, feedback from production)
• Quality Planning
• Quality Trainings
• Lessons Learned Deployment
• External communication with Suppliers
• Monitoring Supplier Performance
Process Improvement (Identifying areas where the process can be improved)
• Controlling Rework and Delays Processes
• Measuring Product
• Inspecting Products (including creating control plans and WIs)
• Tracking, Labelling and booking
Internal Auditing (To carry out the auditing needed for ISO 9001)
• Monitoring Product Conformance
• Inspecting production areas (5S implementation)
Customer General Returns (To register and control returned goods from customers)
• Managing returned products
• Managing Credit Notes
• Reporting to Management
• Root Cause Analysis of returns
• Improvements
Document Control (To control Company documentation availability in QIS)
• Maintaining document register and logging changes
• Making sure work instructions are up to date and controlled as required by ISO9001
Any other duties as required by the business and commensurate with this position.
Skills / Competencies
Attention to detail
Risk based thinking
Problem Solving
Risk assessment
Kaizen techniques/lean thinking
High level of numerical and analytical ability
Able to achieve results by setting high standards and committing to clear objectives
Adaptable to change and varying situations
Ability to show resilience and a flexible approach
Excellent communication and persuasion skills
Computer literate
Full understanding of customer expectations and deliverables with an awareness of the impact of failure/cost of poor quality
Audit skills
As a member of the Quality Assurance Department, producer of water flow regulators, I work to get best quality parts to the customer as quickly and efficiently as possible. During last twelve years of my employment in NEOPERL UK Ltd. I have got knowledge of ISO standards in production and also:
• Experience within the manufacturing industry
• Have proven experience in assembly and testing
• Understand schematic drawings
• Have an innovative and dedicated approach to finding solutions
• Knowledge of ISO and 5S business strategies
• Kaizen - Continual Improvement
• Failure mode analysis
• Process maps
• Process Flow Charts
• Ishikawa Fishbone Diagrams
• 5 Whys
• Waste Management (7 – Wastes)
• Error Proofing (Poka – yoke)
• Total Productive Maintenance (TPM)
• Overall Equipment Effectiveness (OEE)
• Root Cause Analysis (RCA)
I have got deep knowledge and training for main quality inspection tasks. I have got trainings of usage Mitutoyo high precision measurements tools like: SERIES 293 MDC Lite Lightweight Micrometre, SERIES 570 HDS Digimatic Height Gauge, Mitutoyo callipers, Mitutoyo Quick Vision – non-contact measurement system. I have got training of programming and setting from OMRON (three cameras vision sensors system implemented to inspection machine). I have experience in work in QC Lab (First Off testing and measurements) and I know possible defects which can be found in all stages of production. My everyday duties included controlling and testing final products and reporting about any defective batches of regulators which do not reach specification standard of flow rate and also:
• Controlling assembly and test of final products
• Inspection of incoming components checking for defects and imperfections from mould shop and suppliers
• Testing assembled products to strict flow rate criteria required by customer
• Carrying out quality inspections at all stages of the assembly process
• Creating and completing documentation and procedures to improve quality standards
• Using test results to find reasons of fault
• Working within clean room environments (5S)
I was working as a team leader of up to 12 members of Final Inspection Department. I was responsible for organization and supervising everyday tasks and reach 'On Time Delivery' benchmarks. One of my main duties was control and coordination of work flow between Assembly Department, Final Inspection and Despatch Department to achieve right number of orders set up for despatch by Sells Department. I am responsible for reporting to QC Manager about assembly fails, customer returns, suppliers’ defects and everyday correspondence to all departments including Production Manager, Sales Manager, Planner.
Saving Water and Energy Flow Regulators
Get 30% Off